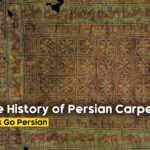
The History of Persian Carpets and Their Influence on World Culture and Art
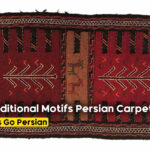
Decoding Traditional Motifs and Designs in Persian Carpets
Hand-woven Persian carpets are more than just beautiful floor coverings; they are pieces of art, crafted through a meticulous process that has been honed over centuries. The journey from raw wool to a finished Persian carpet is a labor-intensive and skillful endeavor, involving various steps that ensure the unique quality and durability of each piece. In this blog post, we will explore the detailed stages of producing a Persian carpet, from selecting the materials to the final product.
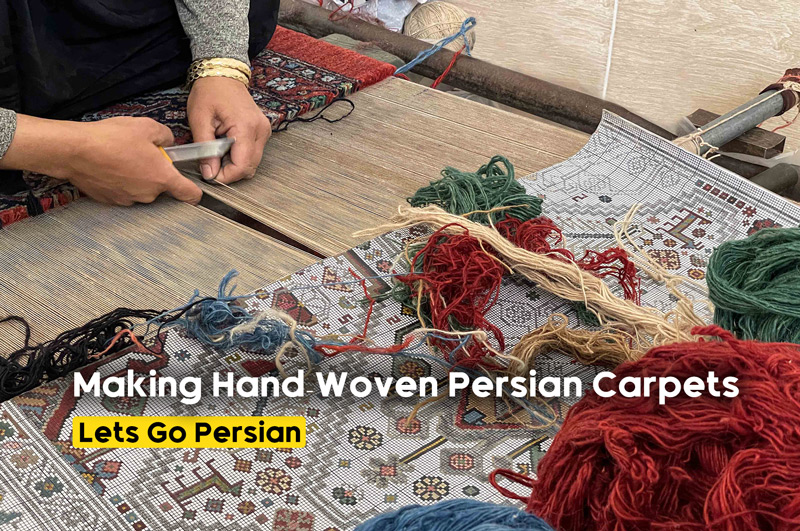
The Process of Making Hand-Woven Persian Carpets
Step 1: Selecting the Materials
Wool, Silk, and Cotton
The choice of material is fundamental to the quality of a Persian carpet. The most commonly used fibers are wool, silk, and cotton, each contributing to the texture, durability, and sheen of the finished product.
- Wool: Persian carpets are typically made from high-quality wool sourced from local sheep. Wool is prized for its softness, durability, and resilience.
- Silk: Often used in finer carpets, silk adds a luxurious sheen and allows for more intricate designs. Silk carpets are usually more delicate and are considered premium products.
- Cotton: Used for the warp and weft, cotton provides a sturdy foundation for the knots and helps maintain the carpet’s shape.
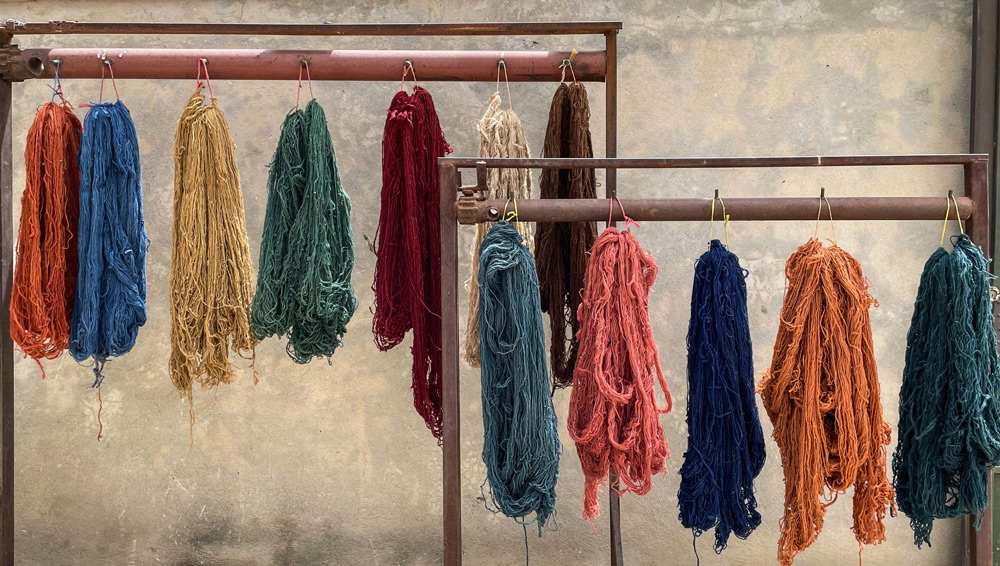
Carpet wool
Dyeing the Yarn
The yarn is dyed before the weaving process begins. Natural dyes are traditionally used, derived from plants, insects, and minerals, which give Persian carpets their vibrant and long-lasting colors.
- Indigo: Produces shades of blue.
- Madder root: Used for reds.
- Pomegranate skins: Create yellow tones.
The dyeing process requires skill and experience to ensure consistent color throughout the yarn and to produce the subtle variations that give the carpet depth and character.
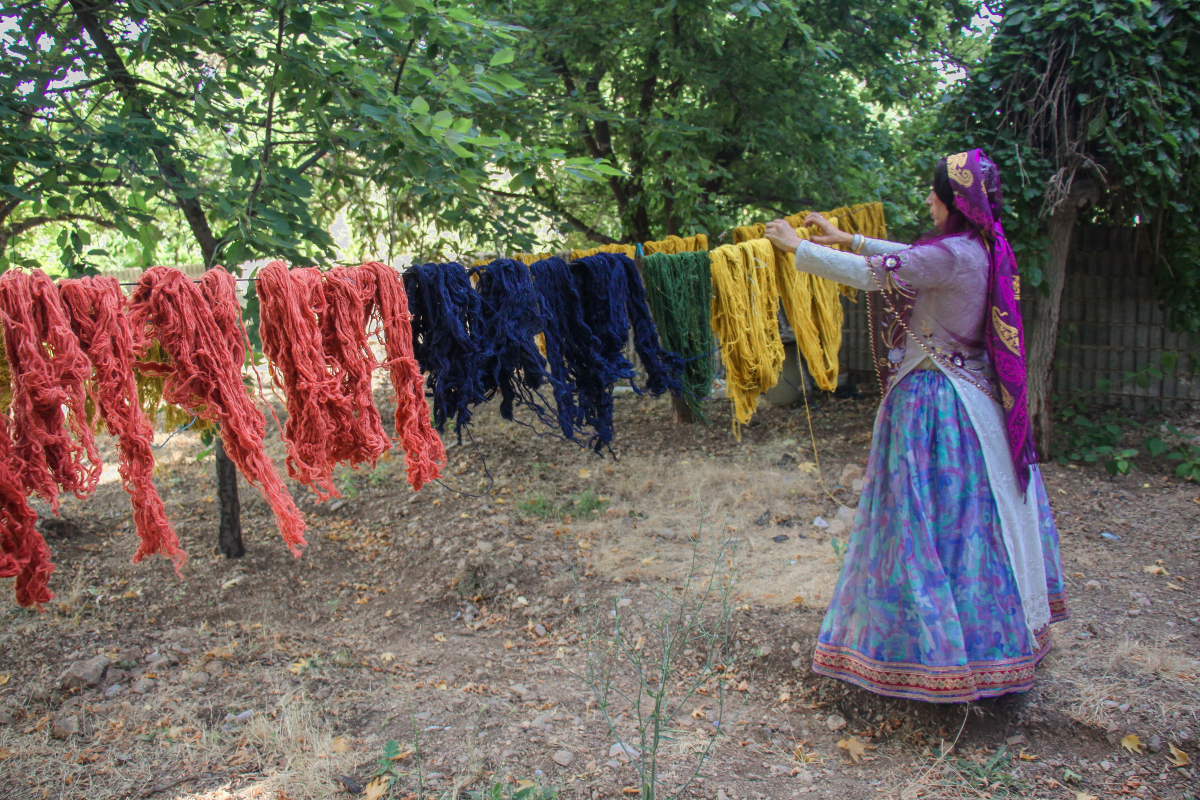
Dyeing the Yarn
Step 2: Designing the Carpet
Traditional Patterns and Symbols
The design of a Persian carpet is often based on traditional patterns passed down through generations. Each region in Iran has its distinctive style and motifs, many of which are deeply symbolic.
- Medallion patterns: Central circular or oval designs symbolizing the sun.
- Floral and garden themes: Represent paradise and the natural world.
- Geometric and tribal patterns: Associated with nomadic cultures, using simple yet striking forms.
Designs are often created on a grid paper by a master weaver, who carefully plans every knot before the weaving process begins. Some designs are passed down orally, especially in nomadic cultures.
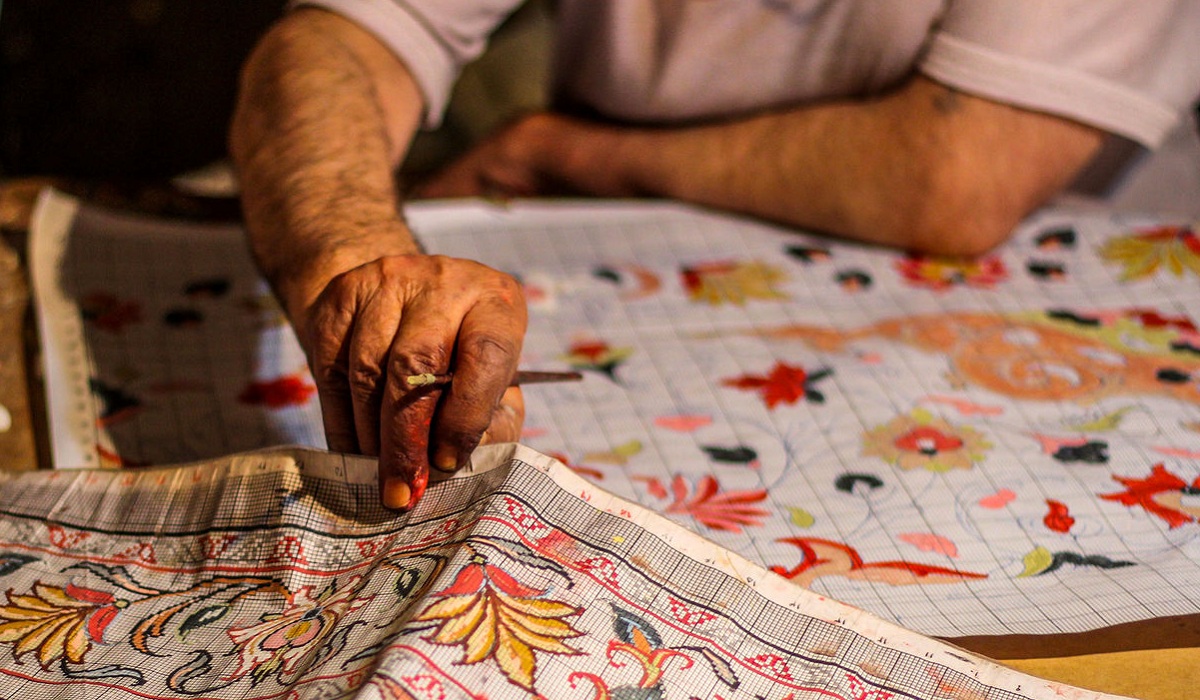
Designing the Carpet
Step 3: Weaving the Carpet
Setting up the Loom
The loom is the primary tool for weaving a Persian carpet. Two types of looms are typically used:
- Vertical looms: Often used for larger or more intricate carpets.
- Horizontal looms: Preferred by nomadic weavers for their portability.
The warp threads (vertical threads) are stretched tightly across the loom, forming the base of the carpet.
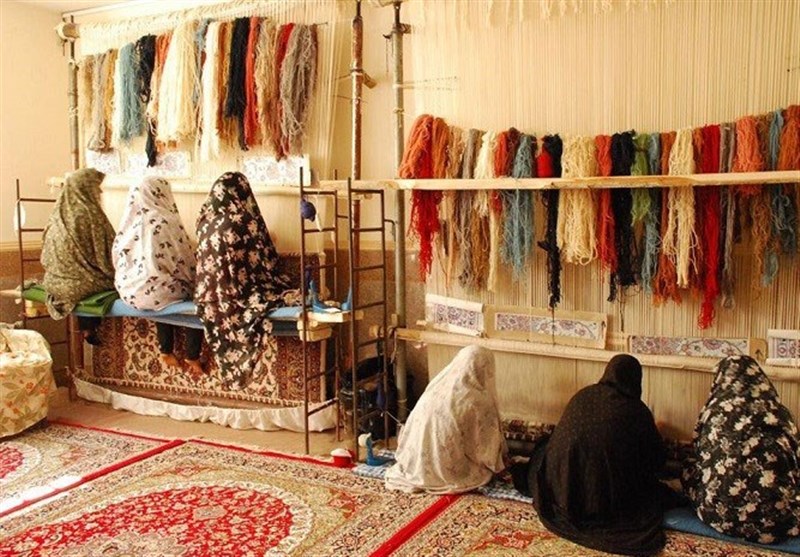
Weaving the Carpet
Knotting Techniques
The art of knotting is at the heart of Persian carpet making. Two main types of knots are used:
- Persian knot (asymmetrical knot): Allows for more intricate designs and finer details.
- Turkish knot (symmetrical knot): Creates a denser, more durable carpet.
Each knot is tied individually by hand, with precision and patience. Some carpets can have over one million knots per square meter, which is a testament to the time and effort required.
- Weft threads (horizontal threads) are inserted between rows of knots to secure them in place.
- After every few rows, the weaver uses a comb-like tool to press the knots tightly together, ensuring a compact and durable structure.
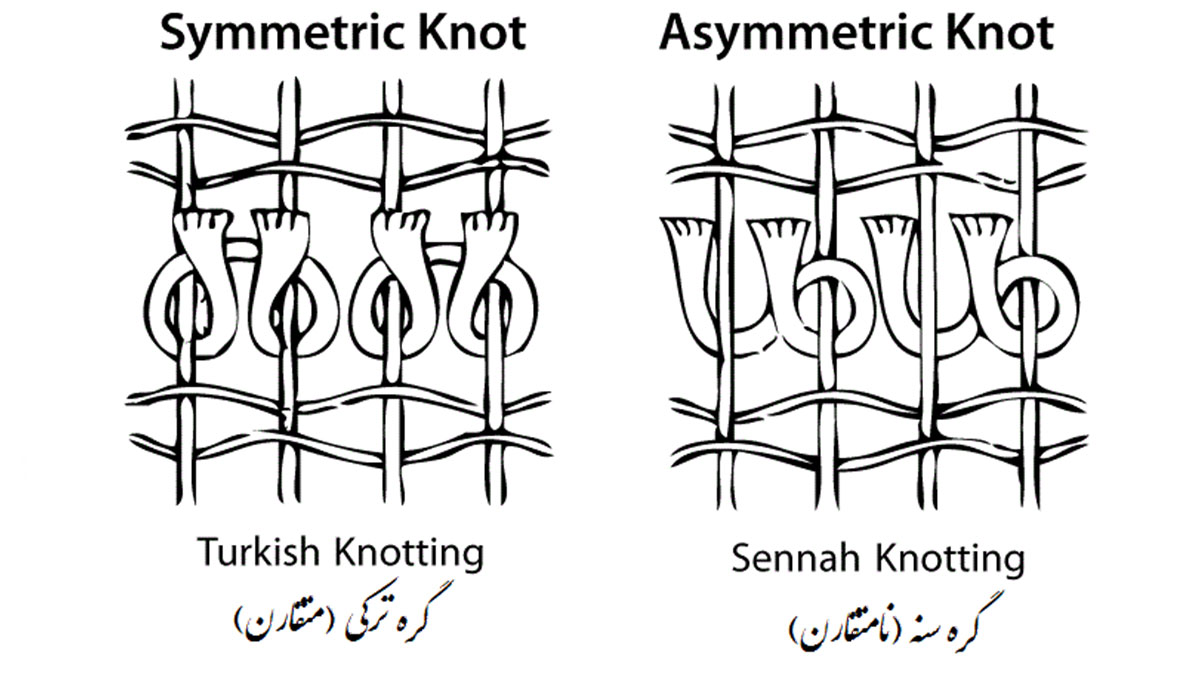
Knotting Techniques
Step 4: Trimming and Washing
Shearing the Carpet
Once the weaving is complete, the surface of the carpet is sheared to ensure a smooth and even pile. This step is critical for bringing out the intricate patterns and designs.
- Pile height: The height of the pile can vary depending on the type of carpet. Shorter piles are often preferred for finer designs, while longer piles may be used in tribal or nomadic carpets.
Washing the Carpet
The newly woven carpet is washed to remove any dust, excess dye, or oils that may have accumulated during the weaving process. Washing also enhances the luster and brightness of the colors.
- Gentle washing: Traditional methods use natural soaps and water to clean the carpet without damaging the fibers.
- Sun drying: The carpet is laid flat in the sun to dry, which helps the colors set and adds to the vibrancy of the finished product.
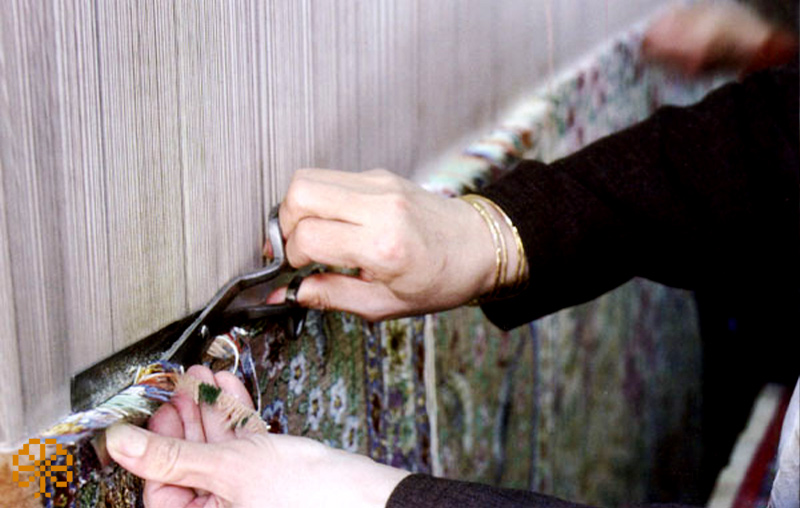
Trimming and Washing
Step 5: Final Touches
Finishing and Binding
After washing, the edges of the carpet are bound to prevent unraveling. This is done by hand, using a strong thread to secure the outermost weft threads.
- Fringe: In many Persian carpets, the fringe is left as a decorative element, but it is also functional, as it is part of the warp threads.
- Edge binding: The sides of the carpet are reinforced with stitching to ensure durability and prevent fraying over time.
Inspection and Quality Control
Before a Persian carpet is considered complete, it undergoes a final inspection to ensure there are no flaws or irregularities in the weaving, colors, or patterns. Only after passing this quality control can the carpet be sold.
Conclusion
The process of making a hand-woven Persian carpet is an intricate and time-consuming journey that combines traditional techniques with artistic mastery. From the selection of raw materials to the final product, each stage requires skill, patience, and attention to detail. Persian carpets are not only functional items but also cultural artifacts that reflect the rich history and artistic heritage of Iran. Their beauty, craftsmanship, and durability ensure that they remain prized possessions in homes around the world.